Our process & work
Vaccum / Thermoforming
Vacuum forming is where a sheet of plastic is heated to a forming temperature, stretched onto a single-surface mold, and forced against the mold by a vacuum. This process can be used to form plastic into permanent objects. Normally draft angles are present in the design of the mold to ease removal of the formed plastic part from the mold.
Relatively deep parts can be formed if the sheet is mechanically or pneumatically stretched prior to bringing it into contact with the mold surface and applying vacuum.
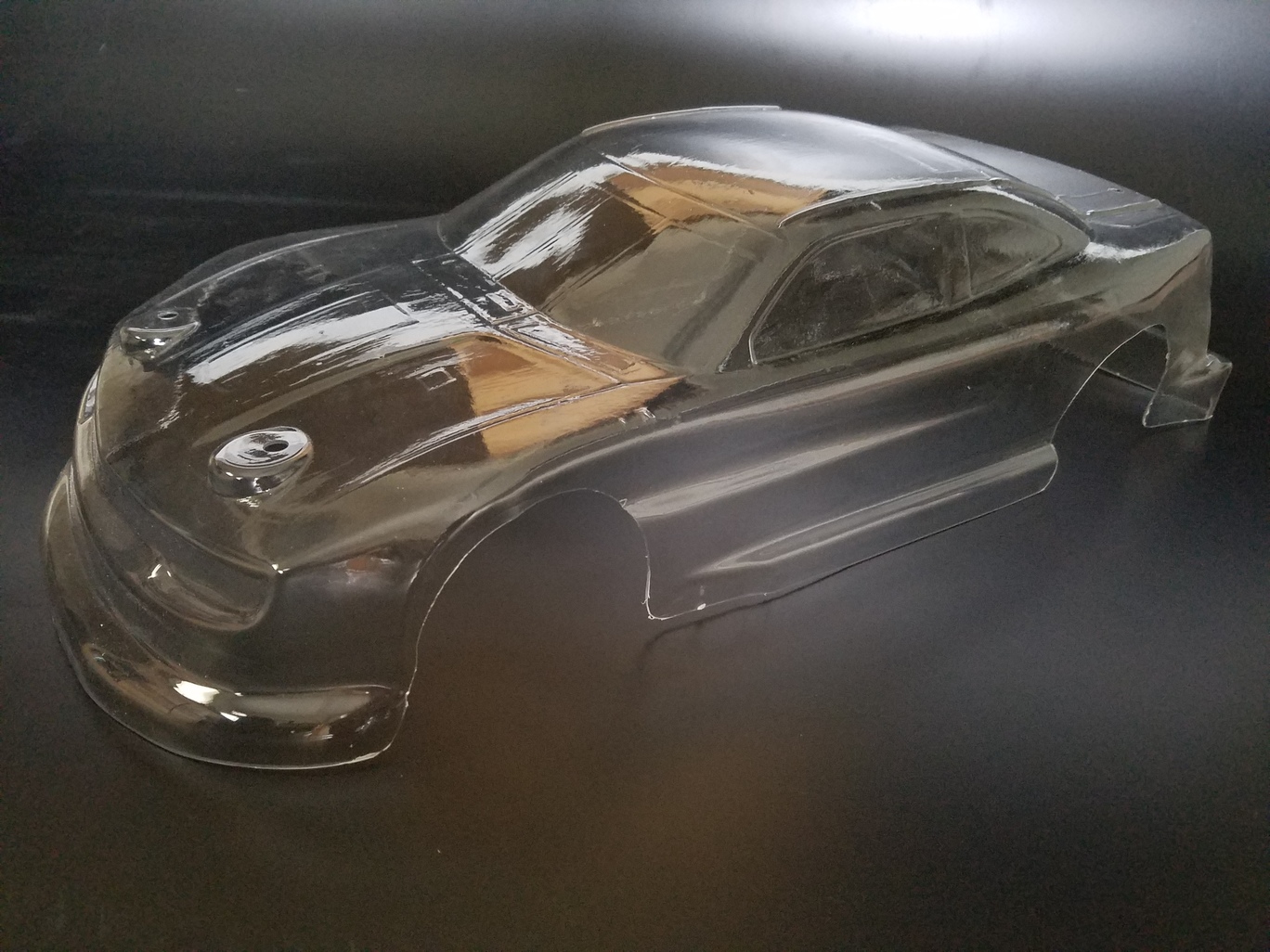
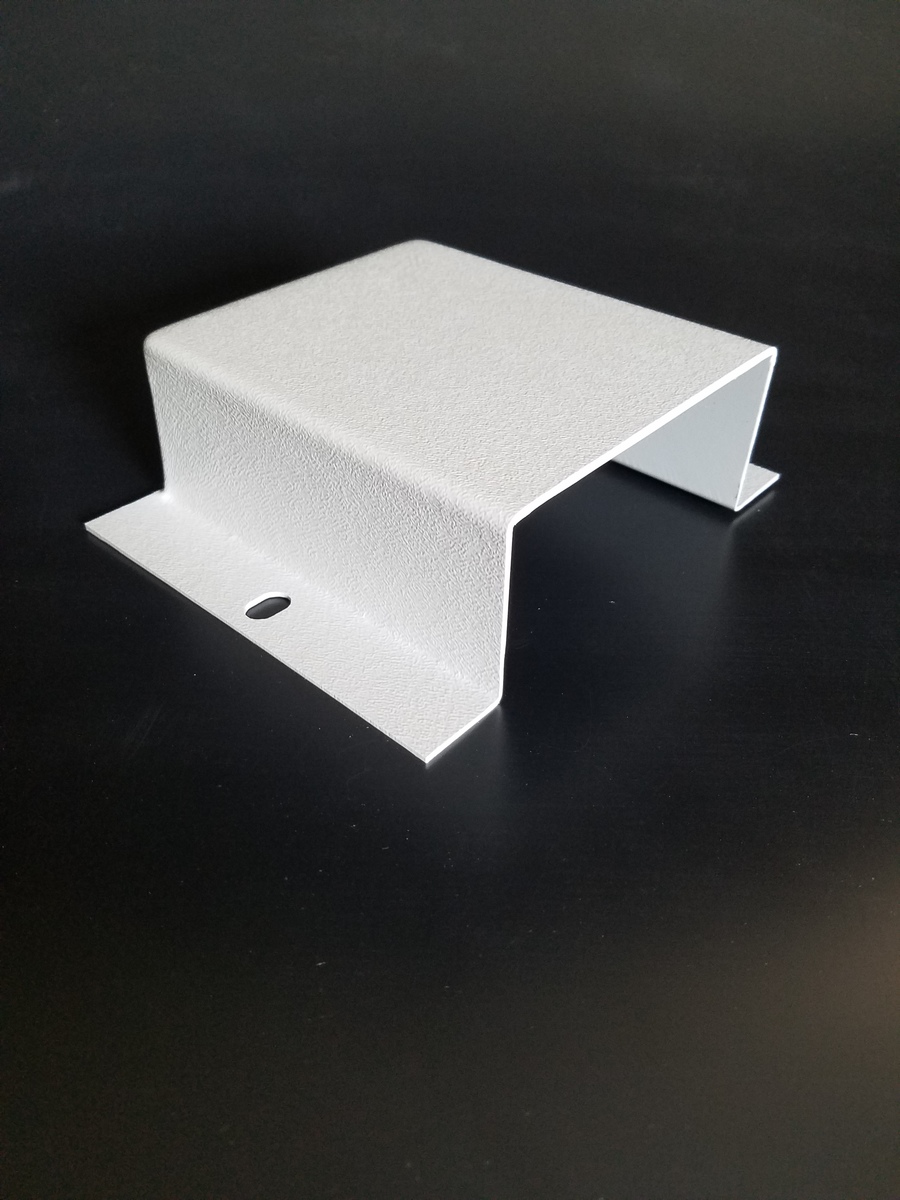
Vacuum / Thermoforming
Suitable materials for use in vacuum forming are conventionally thermoplastics, for example High Impact Polystyrene, and ABS. The plastic is molded around a wood, composite or cast or machined aluminum mold, and can form to almost any shape. Vacuum forming is also appropriate for transparent materials such as Acrylic, and Polycarbonate, which are widely used in applications for aerospace, automotive, merchandising and POP displays.
Vacuum / Thermoforming
Original equipment manufacturers (OEMs) utilize heavy gauge vacuum formed components for production quantities in the range of 250–3000 units per year. Vacuum-formed components can be used in place of complex fabricated sheet metal, fiberglass, or plastic injection molding. Typical industry examples besides product packaging include: fascias for outdoor kiosks and automated teller machines, enclosures for medical imaging and diagnostic equipment, engine covers in a truck cab or for construction equipment, and rail car interior trim and seat components. Vacuum formed parts are also often used by hobbyists, for applications such as masks and remote control cars.
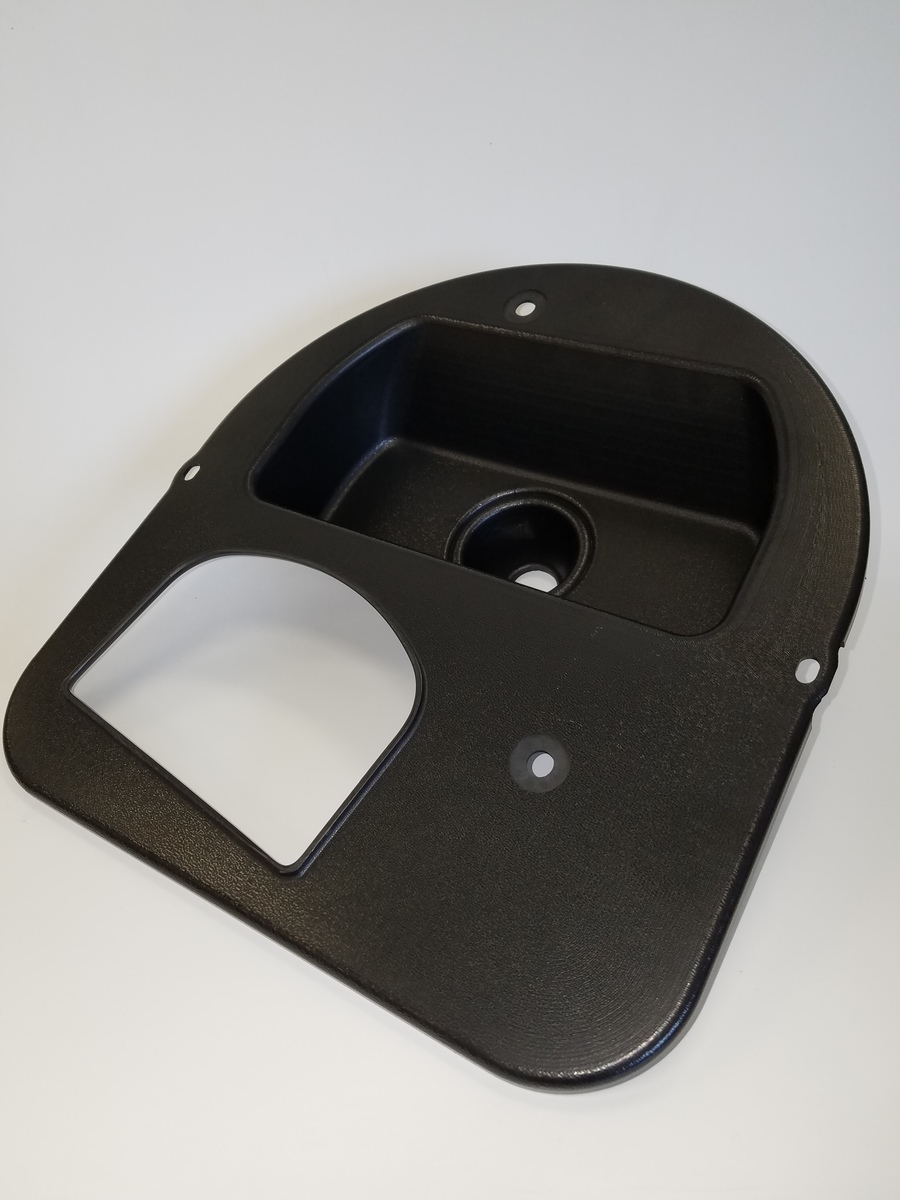
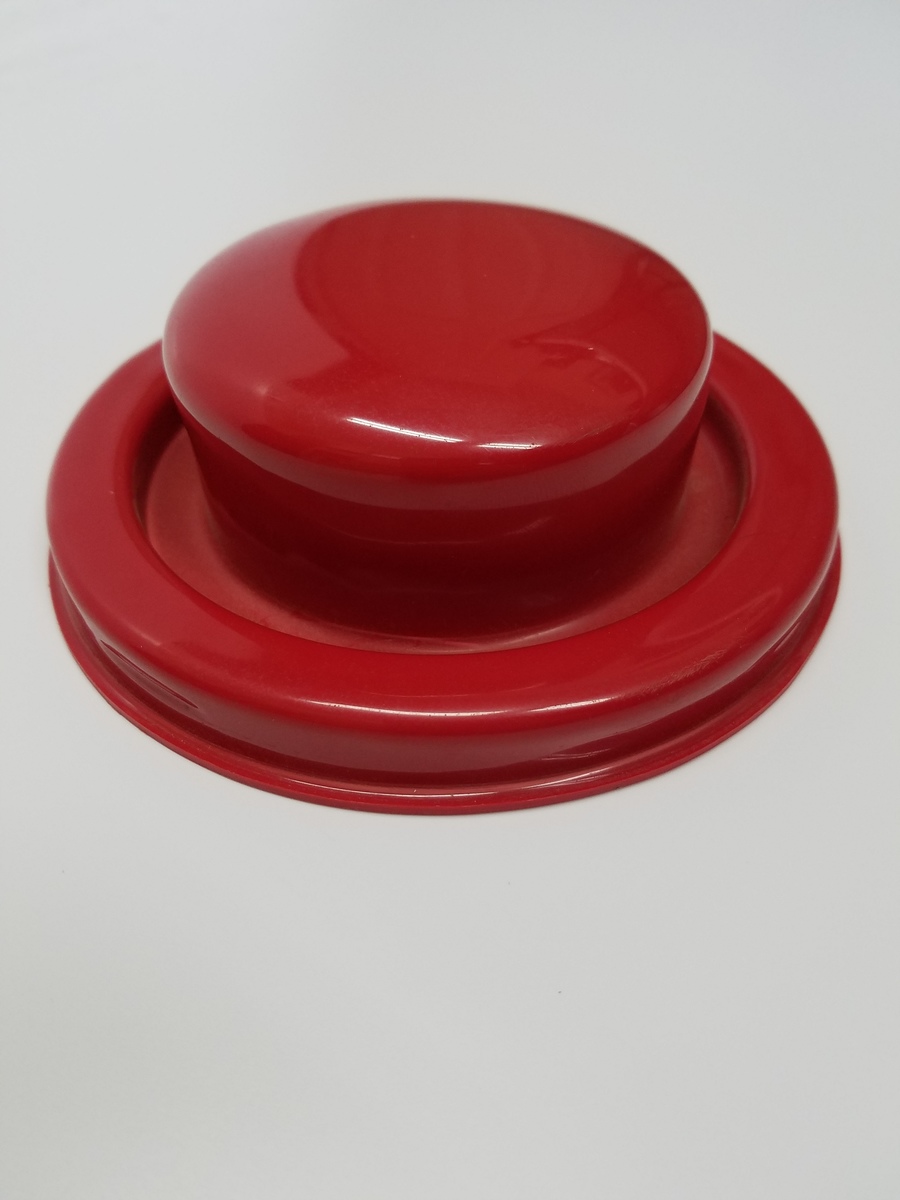
Vacuum / Thermoforming
Wood patterns are a common material used to make vacuum form molds from. Wood is relatively inexpensive and allows the customer to make changes to the design easily. The number of samples that one is able to get from any pattern depends on the size of the part and the thickness of the material. Once the specifications of the part have been met, the pattern is then used to create a ceramic composite mold, or cast aluminum mold for regular production.
Composite molds are a lower cost alternative to cast or machined aluminum molds. Composite molds are typically made from filled resins that start as a liquid and harden with time. Depending on the application, composite molds can last a very long time and produce high quality parts. Cast aluminum molds are cast at a foundry and typically have temperature control lines running through them. This helps to set the heat of the plastic being formed as well as speed up the fabrication process. Aluminum molds can be male or female in nature, and can also be used in pressure forming applications.
Machined aluminum molds are like cast aluminum , but are cut out of a solid block of aluminum using a CNC machine and a CAD program. Typically, machined aluminum is used for shallow draw parts out of thin gauge material. Applications may include packaging and trays.
Vacuum / Thermoforming
Drilling: If simple round holes are the required finish, manually drilling them is a good solution for small quantities. Drilling guides can be used to ensure holes can be drilled quickly in the right place. As this is a labor-intensive method, it is only suitable for small production quantities.
3 or 5 Axis CNC: Cutting with a CNC machine is a very precise method of creating holes & features and trimming a part to a final shape. A CNC router typically produces consistent and high-quality work and improves factory productivity. Unlike a jig router, the CNC router can produce a one-off as effectively as repeated identical production. Automation and precision are the key benefits of CNC router tables. A CNC router can reduce waste, the frequency of errors, and the time the finished product takes to get to market.
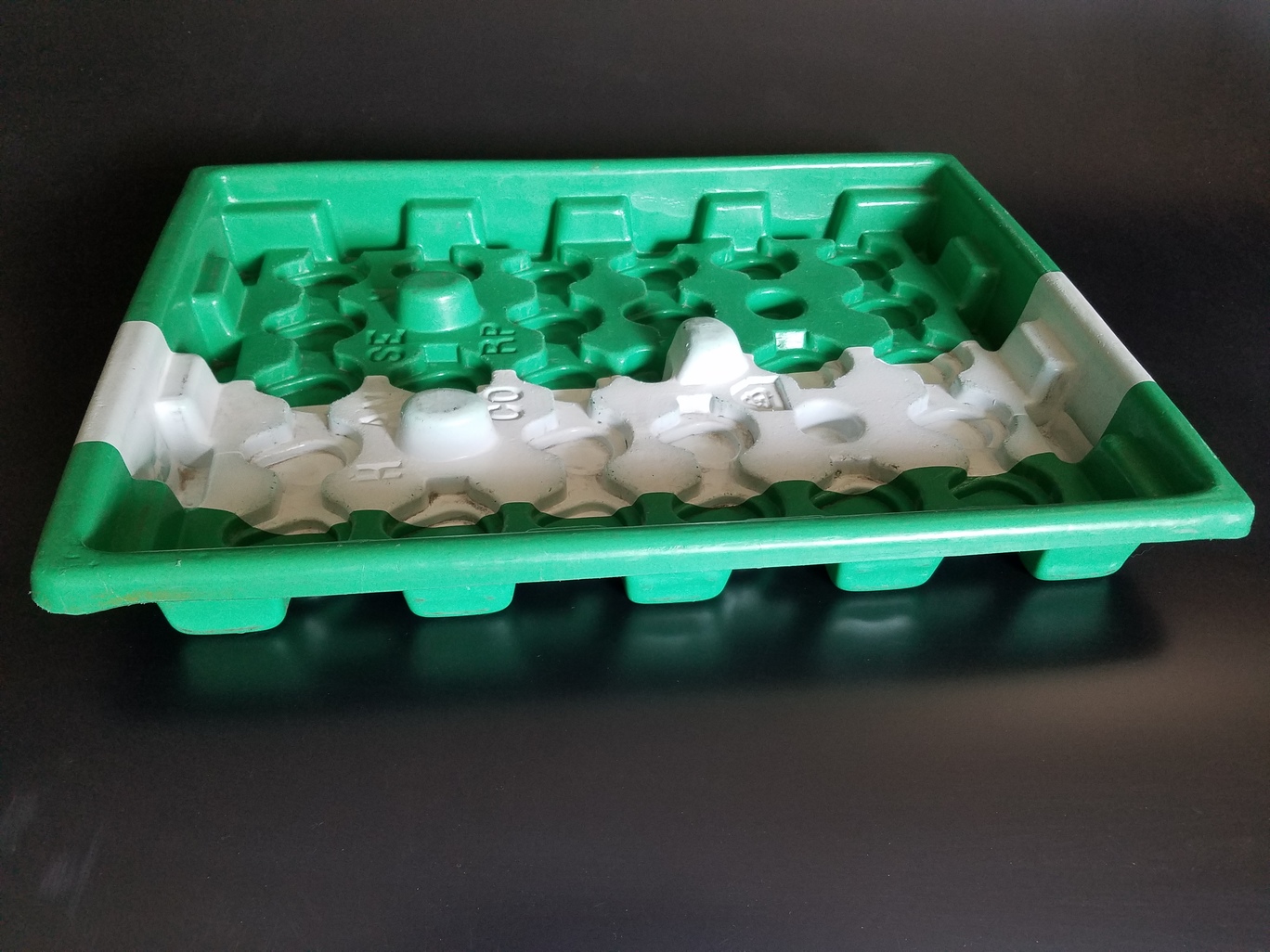